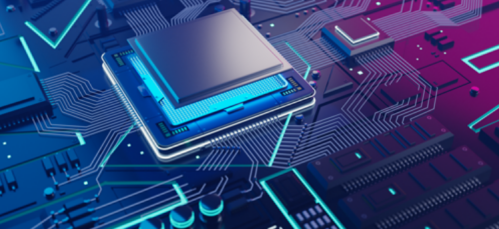
一, 半导体材料检测
外观检查(光学显微镜) | X-ray 检查 | SAT 检查 |
SEM-EDS 电子显微镜 | IR Reflow 回流焊 | Pre-Condition Test/ MSL |
De-cap开封 | Cross-section 截面研磨 | P-lapping 分析 |
Dual beam FIB | WBS 绑线拉剪切力 | WBP 绑线拉力 |
二,半导体产品检测
加速环境应力试验 | 加速寿命模拟试验 | 封装完整性测试 |
电性验证测试 | 空腔封装完整性测试 | 无损分析 |
破坏性分析 | 故障定位分析 | ESD-HBM/MM/CDM |
|
|
|
三,汽车半导体认证测试AEC-Q
测试标准:AEC-Q100(集成芯片)、AEC-Q103(MEMS)、AEC-Q101(分立半导体)、AEC-Q104(多晶圆及模组体)、AQG-324(功率器件)、AEC-Q102(分立光电半导体)、AEC-Q200(被动元器件)
封装IC:加速环境应力测试、加速寿命模拟试验、封装凹陷测试
四,半导体失效分析
失效分析是为确定和分析失效器件的失效模式、失效机理、失效原因和失效性质而对产品所做的分析和检查。
通过失效分析可以验证器件是否失效,识别失效模式,确定失效机理和失效原因,根据失效分析结论提出相应对策,包括器件生产工艺,设计,材料,使用和管理等方面的有关改进,以便消除失效分析报告中所涉及到的失效模式或机理,防止类似失效的再次发生。
失效分析在提高产品质量、技术开发、产品修复及失效事故等方面具有很强的实际意义:非破坏性分析作为失效分析中的第一站,能够快速有效地帮助客户做初步的判断,同时为进一步分析收集更多的失效信息;破坏性分析是对元器件样品进行一系列寻找失效机理分析与实验的过程,并为客户提供确定失效是偶然性还是批量性的依据,进而依据结论为客户寻找改善措施。
常规方法如下:
1. I-V curve tracer/电测 | 6. Cross section/截面研磨 |
2. Visual inspection/外观检查 | 7. EMMI/OBIRCH/InGaAs |
3. X-ray/CT检查 | 8. Delayer去层 |
4. SAT/超声波扫描检查 | 9. SEM/EDS/成分分析 |
5. De-cap/开封检查 | 10. DB-FIB双束聚焦离子束 |
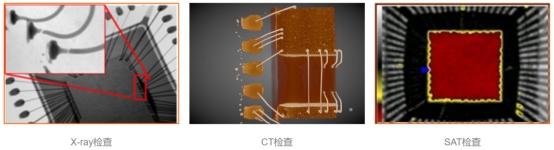
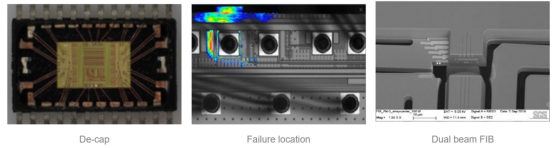